Our Tech
We’re working to help brands adopt more sustainable materials and waste management practices.
We develop engineered microorganisms to turn industrial byproducts into low-footprint, bio-based biodegradable plastic resins and additives.
Our microbes are unique in their ability to produce complementary biomaterials in a single fermentation process, and our proof of concept uses dairy processing byproducts to co-produce bio-based, biodegradable plastic resins and pigments.
We want to work collaboratively to convert your byproducts into key products for your supply chain, and can assist through the provision of services in waste stream analysis, product/material formulation, and licensing of our fermentation technologies. Please reach out via our contact page if you would like to learn more about the types of projects we’re involved in and services we offer, obtain a quote, or licensing opportunities.
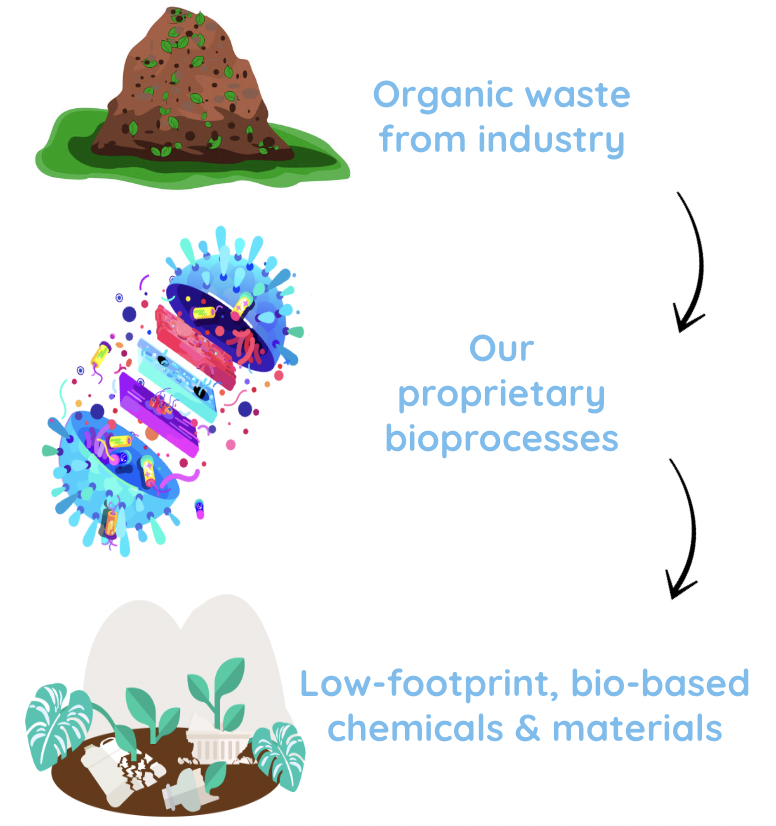
Fermentation in action
Keep Up with Our Latest News
Read Our Last Blog Post:
No Results Found
The page you requested could not be found. Try refining your search, or use the navigation above to locate the post.